development
ソルテックの挑戦。
研究開発技術
研究開発事例: 2022年10月 形彫放電加工機SV8Pによる鏡面放電加工
2018年に導入した三菱電機 超高精度形彫放電加工機SV8Pによる鏡面放電加工を活用することで、従来の手作業によるミガキを必要としない効率的な加工方法を編み出した。
研究開発の狙い・背景
本研究開発事例の狙いは、形彫放電加工機による鏡面放電加工の機能を活用することで生産効率を高めることである。
細かな面粗度が求められるディンプル形状のパンチ製作において、形彫放電加工機で形状を加工した後に、手作業によるミガキ及びエアロラップの仕上げを行っていた。加工時間に関して、形彫放電による形状加工が4.5時間、ミガキが2.5時間を要する。
そこで形彫放電加工機の鏡面放電加工の機能を活用し、放電加工の自動時間が増える代わりに、手作業のミガキの時間を短縮させて、加工の効率化を図った。
行ったこと
形彫放電加工機
[A]三菱電機 EA8PV ADVANCE (2012年導入)
[B]三菱電機 SV8P (2018年導入)
CNC表面粗さ・輪郭形状測定器
[C]ミツトヨ FORMTRACER Extream SV-C4500-S4
上記2台の形彫放電加工機[A], [B]で鏡面放電加工後に、表面粗さ測定器[C]を使用して面粗度を測定した。目標の面粗度はRz 0.5µm(Ra0.06µm)以下を設定する。
結果
[A]では、ムラが生じて不均一な加工面になり、仕上げ面には多数のマイクロクラックが観察された。
一方[B]では加工面にムラがなく均一で良好な仕上げ面を得ることができ、目標であるRz 0.5µm(Ra0.06µm)以下の面粗度が得られた。加工時間は粗加工から鏡面加工まで8時間であった。また手作業のミガキが不要になり、0.5時間のエアロラップのみの仕上げで十分な鏡面を得ることができた。
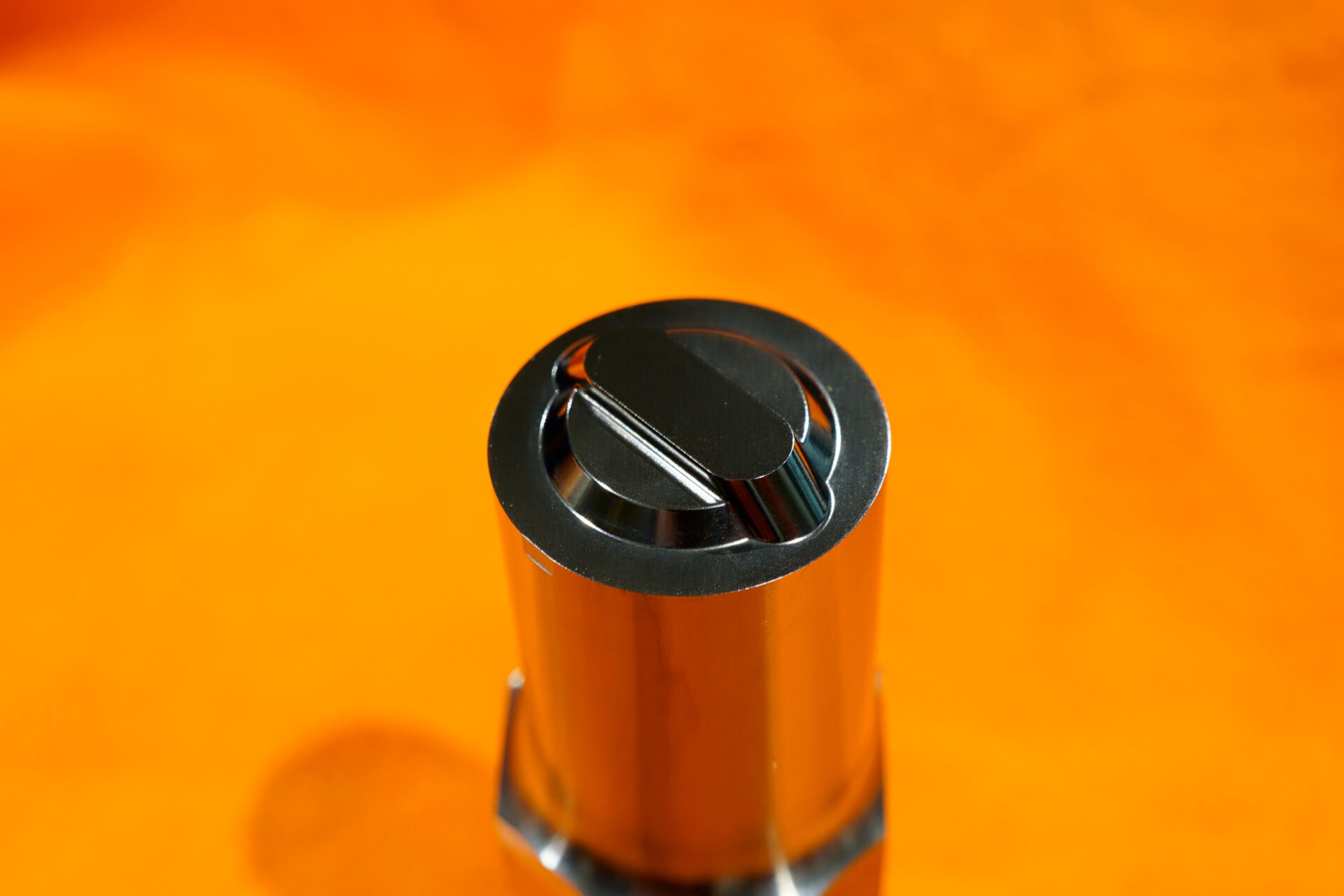
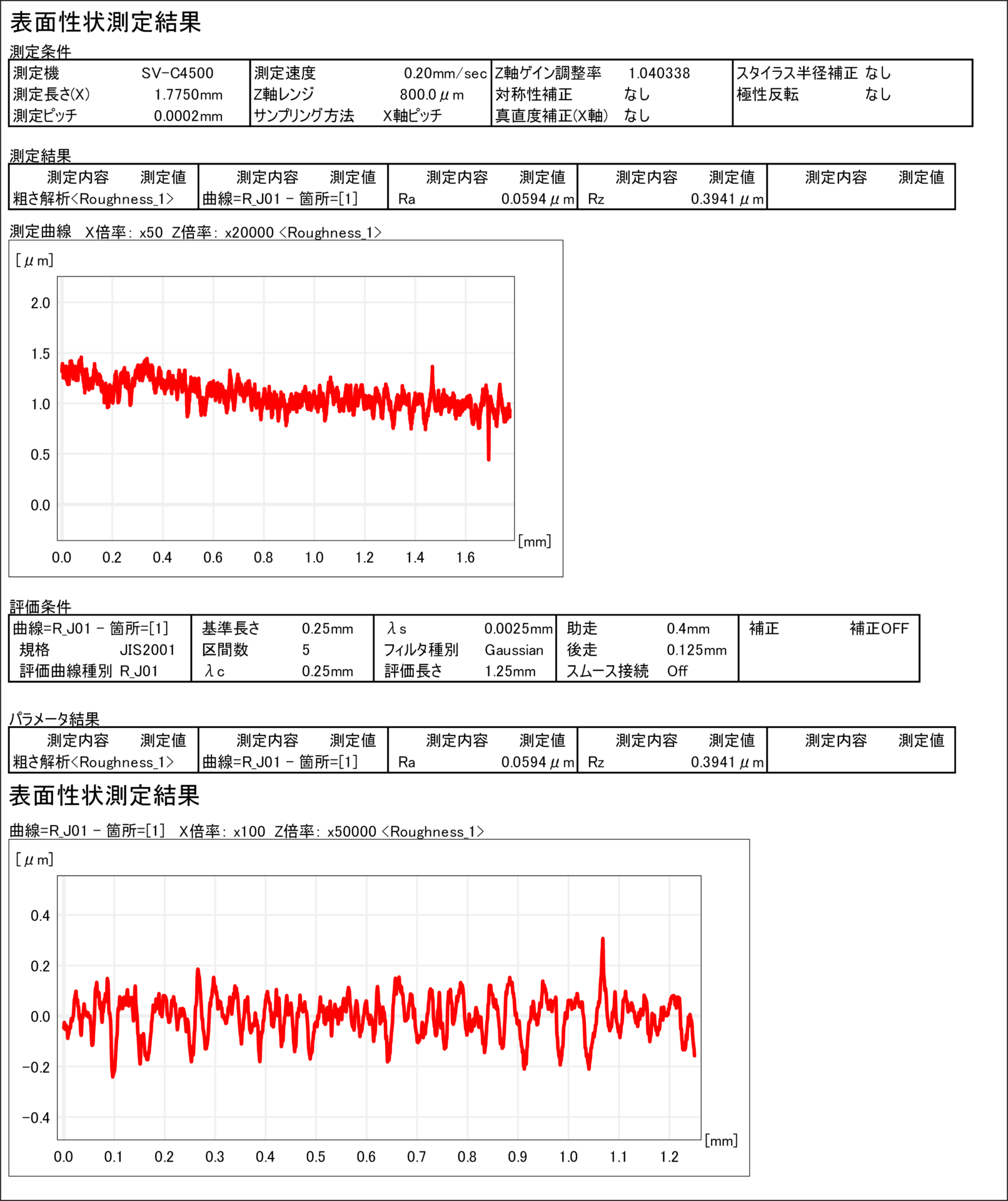
考察
形彫放電加工機[B]の鏡面放電加工により、目標の面粗度を満たすディンプル形状のパンチ製作に成功した。全体の加工時間は増えてしまったものの、手作業によるミガキの時間を大幅に削減することができ、生産効率の向上に貢献した。夜間の自動運転加工で日毎に2本のパンチが製作可能である。問題点を挙げるとすると、鏡面放電加工は電極がより消耗しやすいため、加工精度を維持するためには、より多くの電極を必要とすることである。